Smartwatch Factories is a smartwatch factory in China. In terms of smartwatch production, it has formed a huge industrial chain, covering multiple links from design, R&D, raw material procurement to production, assembly, testing and quality control.
Welcome to visit our smartwatch factory in China to learn about our production process, including smartwatch factory equipment, work flow, etc.

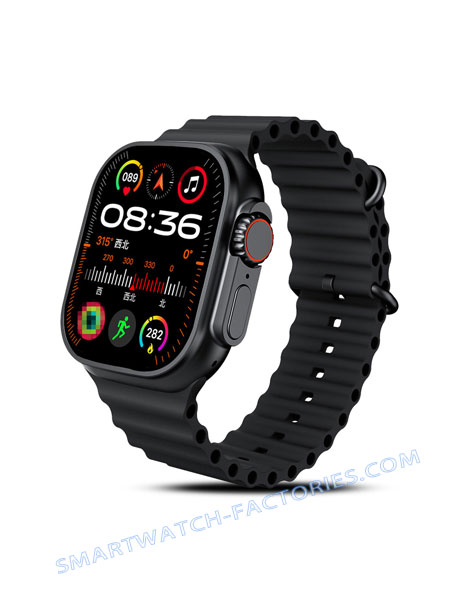
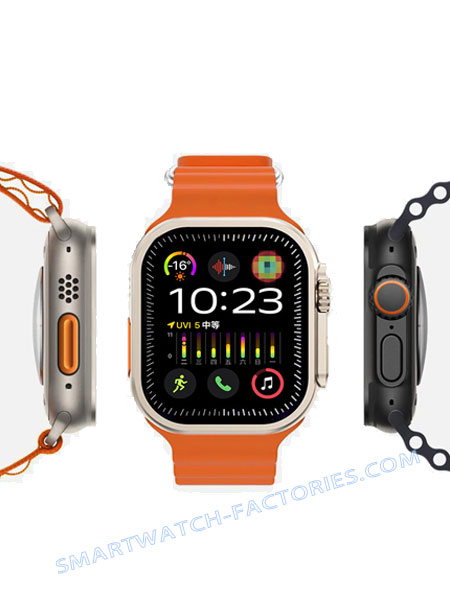
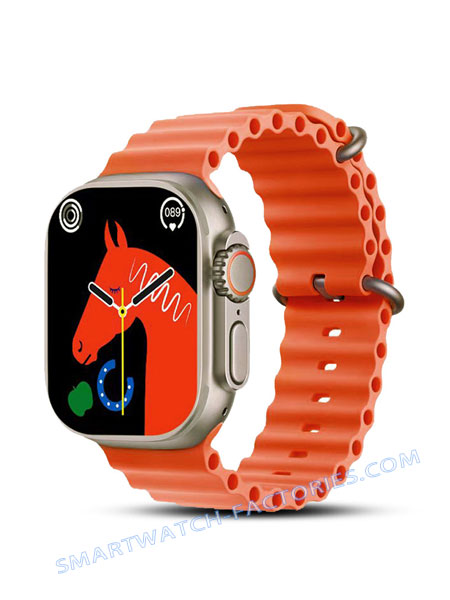
Factory Overview
Located in Shenzhen, Guangdong Province, China, Smartwatch Factories is a well-known smartwatch factory. It is a leader in the industry with advanced production equipment and a complete production management system.
Our factory focuses on the R&D and production of smart wearable devices such as smartwatches and smart bracelets. The annual output is huge, and the products are exported to domestic and foreign markets, including the United States, Russia, Brazil, India, Spain, etc.
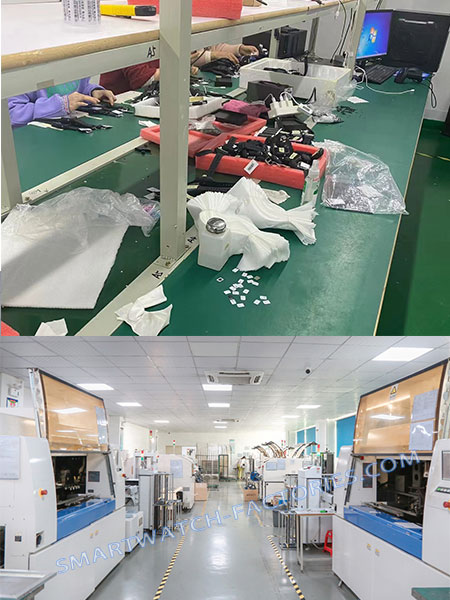
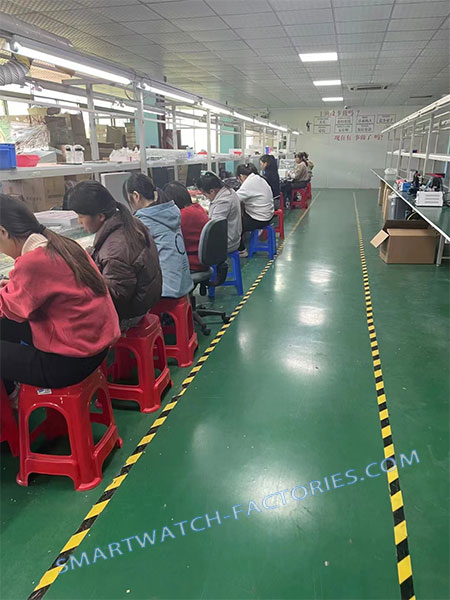
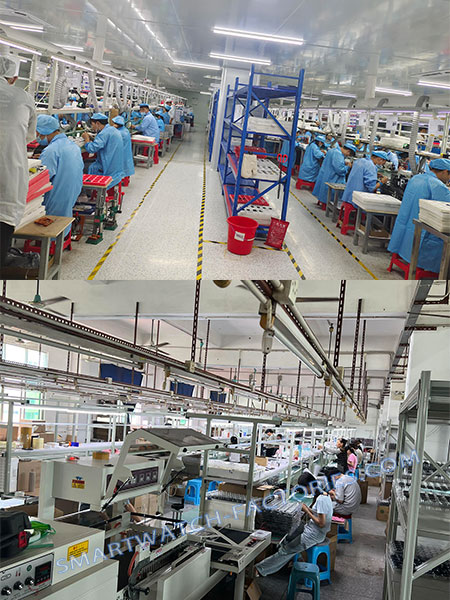
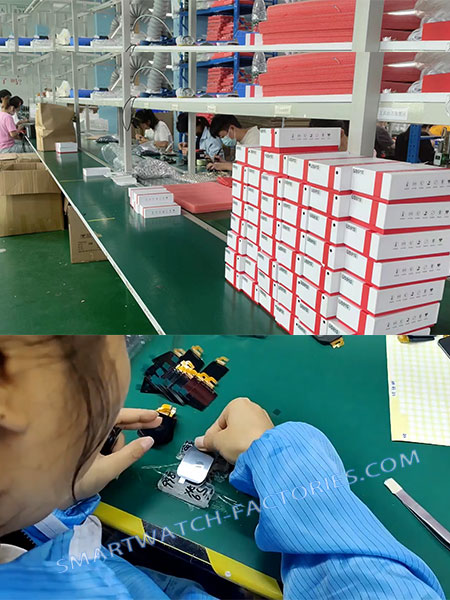
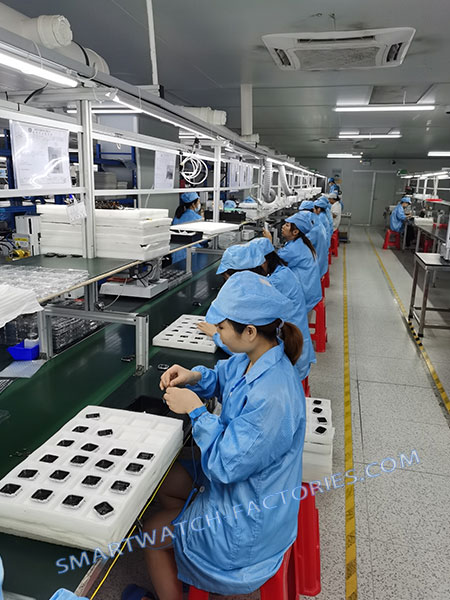
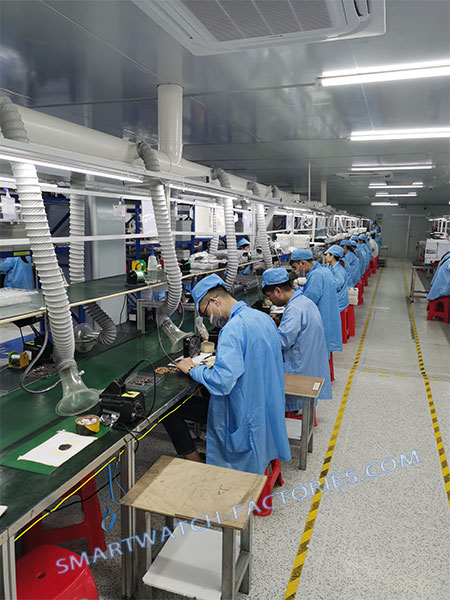
Factory Equipment
1. Automated production line
When entering the factory, the first thing that comes into view is a series of highly automated production lines. These production lines integrate a variety of automated equipment, including automatic film laminating machines, CNC machine tools, automatic spraying machines, automatic welding machines and automatic assembly machines, which greatly improves production efficiency and quality stability.
- Automatic film laminating machine: used to precisely fit the protective film on the display screen of the smart watch, avoiding bubbles and skew, and ensuring the appearance quality of the product.
- CNC machine tool: responsible for processing various parts of the watch, such as metal watch cases, bezels, etc., through precise engraving and milling, to achieve the manufacture of complex shapes and fine textures.
- Automatic spraying machine: spray various colors and coatings on the watch case and strap to achieve personalized appearance effects, while ensuring the uniformity and durability of the coating.
- Automatic welding machine: used to weld circuit boards, batteries and other components inside the watch to ensure the stability and reliability of the connection.
- Automatic assembly machine: automatically assemble various parts (such as display screens, circuit boards, batteries, straps, etc.) into a complete watch, reducing manual operations and improving assembly accuracy and efficiency.
2. Inspection and testing equipment
At the end of the production line, various inspection and testing equipment are set up for comprehensive quality inspection of finished products. These devices include:
- Function tester: simulates various usage scenarios of watches to detect whether their functions are normal, such as time display, heart rate monitoring, Bluetooth connection, etc.
- Waterproof tester: tests whether the waterproof performance of watches meets the standards by simulating different water depths and pressure environments.
- Drop tester: simulates the accidental fall of watches to test their fall resistance and structural stability.
- High-precision measuring instruments: such as vernier calipers, microscopes, etc., used to measure whether the accuracy and appearance dimensions of watches meet the standards.
Workflow
1. Design and R&D
Before the production of smart watches, product design and R&D are required first. Designers draw the appearance and internal structure drawings of the products according to market demand and consumer preferences. The R&D team is responsible for the design of circuit boards, the development of software, and the realization of various functions. This stage requires a lot of human and material resources to ensure the innovation and competitiveness of the products.
2. Raw material procurement
The quality of raw materials directly affects the final quality of the product. Therefore, the factory will strictly screen the suppliers of raw materials for smart watches to ensure that high-quality raw materials are purchased.
These raw materials include display screens, batteries, circuit boards, casings, straps, etc. The purchasing department will place purchase orders in a timely manner according to the production plan and inventory situation to ensure the smooth operation of the production line.
3. Production and assembly
After the raw materials are in place, the production line starts to operate. First, various parts are processed and manufactured on CNC machine tools and other equipment. Then, these parts are sent to the automatic assembly line for assembly. During the assembly process, the automatic assembly machine will accurately install components such as display screens, circuit boards, batteries, etc. to the corresponding positions of the watch. At the same time, manual operators will also participate in some delicate assembly work, such as installing straps and adjusting hands.
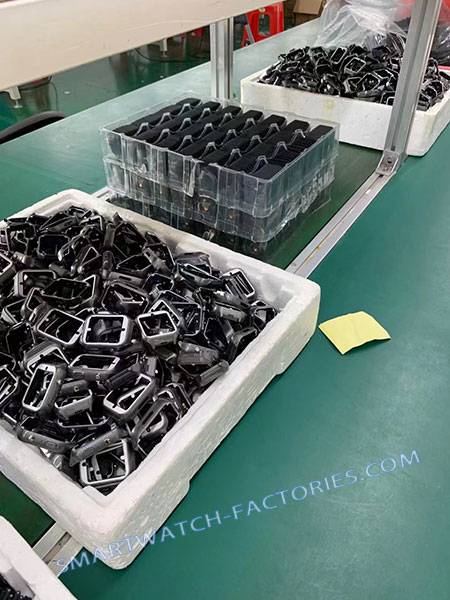
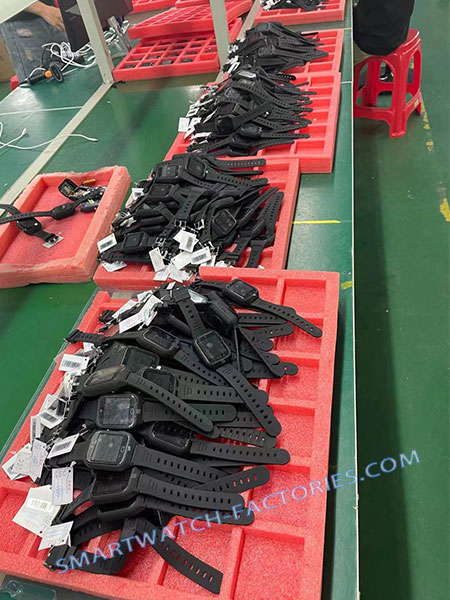
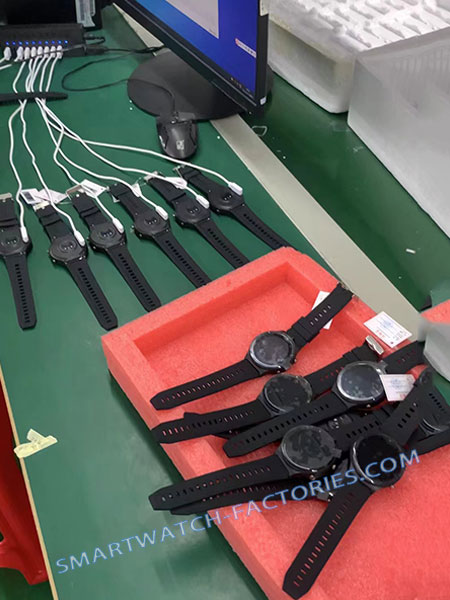
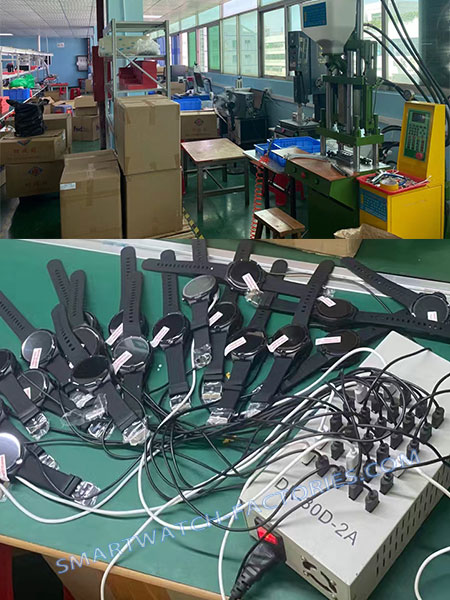
4. Quality control and inspection
After the assembly is completed, the watch will enter the quality inspection link. The inspectors will use various inspection and testing equipment to conduct a comprehensive inspection of the finished product to ensure that the functions of the product are normal, the appearance is flawless, and the quality meets the standards. For unqualified products, they will be returned for repair or scrapped.
5. Packaging and Shipping
Qualified products will be sent to the packaging workshop for packaging. The packaging workshop will pack the watches into exquisite packaging boxes according to the order requirements, and attach accessories such as instructions and warranty cards.
Then, these packaged products will be sent to the warehouse for shipment. Before shipment, the warehouse manager will check the quantity, model, etc. of the products to ensure that they are correct before shipping to customers.

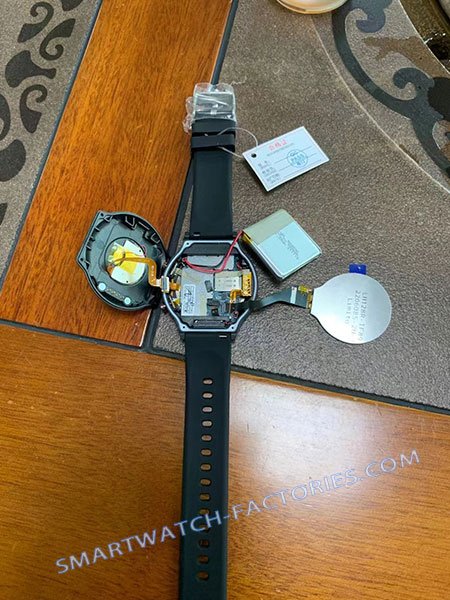
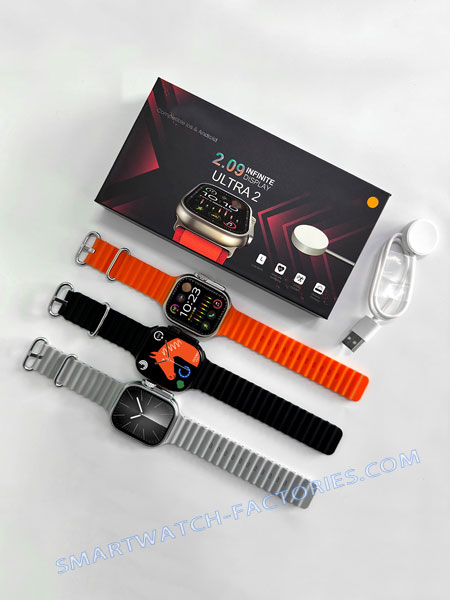
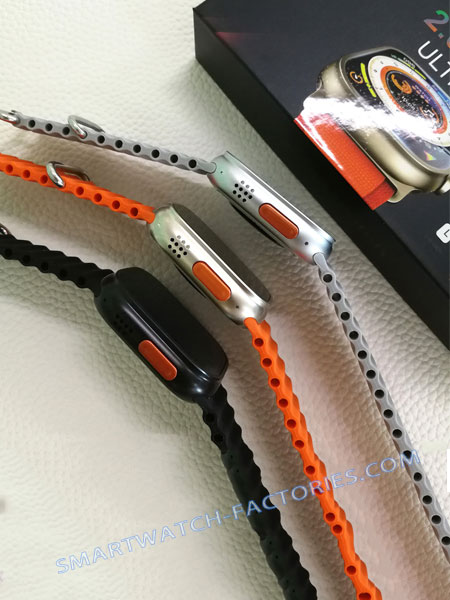
Factory Management
In order to ensure the smooth operation of the production line and the stability of product quality, the factory will take a series of management measures:
- Quality Management System: Establish a complete quality management system to ensure that each link meets international quality standards such as ISO; meet global import and export quality standards.
- Employee Training: Regularly conduct skills training and safety education for employees to improve employees’ operating level and safety awareness.
- Equipment Maintenance: Regularly maintain and maintain production equipment to ensure the normal operation of the equipment and extend its service life.
- Environmental Protection Measures: Take environmental protection measures to reduce pollution emissions and resource waste in the production process and achieve green production.
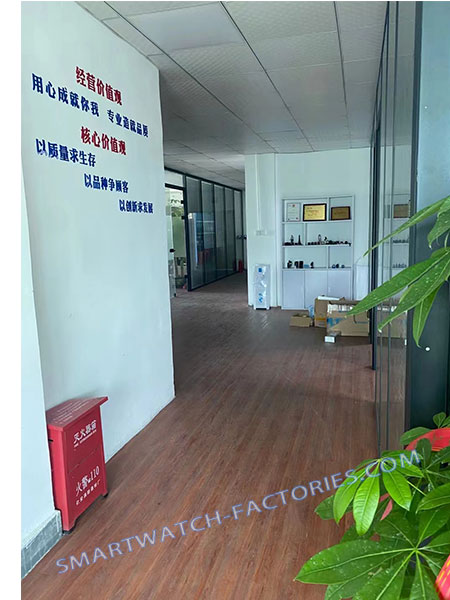
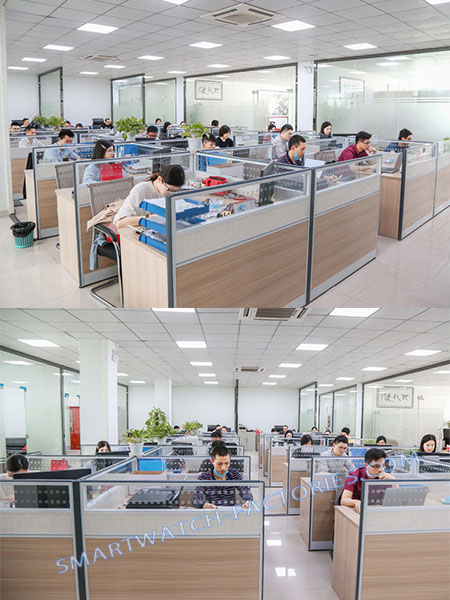
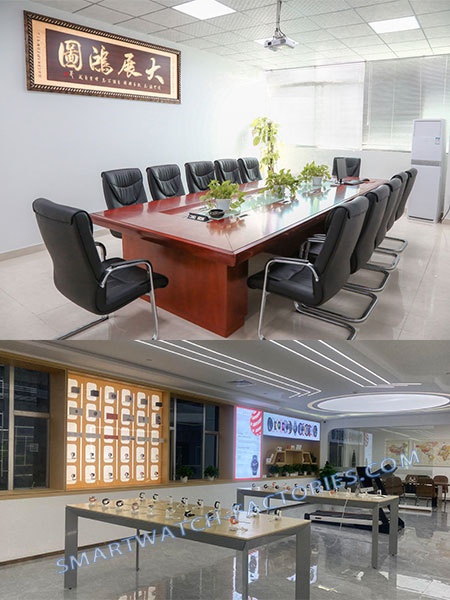
Summary
If you are in China, you can come to visit our factory and you can feel the booming development and huge potential of China’s smart wearable device industry up close.
Smartwatch Factories has advanced production equipment and a complete production management system, which can produce high-quality and high-performance smartwatch products. At the same time, the factory also pays attention to employee training and the implementation of environmental protection measures, laying a solid foundation for the sustainable development of the enterprise.